|
Mechanics of Multiscale Materials |
|
|
|
|
Mechanics of Multi-scale Materials
The Mechanics of Multi-scale Materials research group uncovers the relationships of structures across the full range of engineering scales, from the molecular to the macro. In addition to established practices of nano-scale modeling and large-scale structural mechanics, the research group is bridging the gap between these scales by developing accurate constitutive modeling and characterization of each intermediate level. The research group identifies the critical parameters that lead to success or failure of material for a particular application. For example, to better understand how the material properties of polymer-based structural composites affect airfoil performance, researchers are using advanced modeling and experimental methods to pattern the relevant materials mechanics operating at each scale. Others are working to model structural foam designs for aerospace and automotive products, with the goal of improving thermal insulation, impact absorption, and moment of inertia. Uncovering how the nano- and micro-level mechanics play into the millimeter and meter level structures enables advanced composite materials to be optimized for structural performance.
Through advanced multi-scale modeling, simulation, and experimentation, research is focused on developing methods that will inform emerging technologies including nano-, micro-, and biomedical engineering and science. The Mechanics of Multi-scale Materials research group is well positioned to advance the state-of-the-art in this rapidly emerging field. As functions of intermediate scales between the nano and macro are characterized, novel materials and composites can be created and optimized. Researchers are working on novel experiments, MEMS/NEMS, atomistic and continuum modeling, multifunction materials and devices, microfluidic, tissue engineering, nanostructured material, material characterization, biological transport, cell mechanics and physics-based modeling.
|
Mechanics of Multi-scale Materials Research Group
Current research highlights:
Equivalent-Continuum Modeling of Nanostructured Polymer Composites: Nanostructured polymer composite materials have the potential to provide significant increases in mechanical properties relative to current materials used for aerospace applications. To facilitate the development on nanostructured materials, modeling techniques must be developed that predict the bulk mechanical properties of the composite as a function of the molecular structure of the individual constituents.
Project M-Contact Mechanics in the Human Knee Joint: Using existing finite element model of the human knee joint to study the effects of adding magnets to the knee. The output will determine how the magnets effect the kinematics and contact mechanics of the human knee. This will require an iterative approach because as the kinematics changes, the magnetic field also changes.
Structure and Function of Meniscal Horn Attachments: Menisci function to distribute load and increase stability of the knee joint. Both partial and complete meniscectomy have been shown to increase the incidence of osteoarthritis. Meniscal replacement with allograft, synthetic or tissue engineered replacements, could act to reduce the incidences of osteoarthritis. The success of meniscal replacements depends on their ability to restore normal meniscal function both biologically and biomechanically. Meniscal attachments are critical for proper meniscal function. Since rupture of the horn attachments of the menisci are rare it is likely that a gradient in mechanical and biochemical make-up exists through the attachment. Previous studies have not yet identified the mechanism by which a transition from meniscus fibrocartilage to subchondral bone occurs. The goals of this project are to quantify the relationship between structure and function for meniscal attachments, and to validate a fibril-reinforced finite element model of the meniscal horn attachments. Specifically the project will 1) determine the local fluid pressures during both physiological loading level and failure testing using a fibre-optic pressure microsensor, 2) quantify the collagen orientation in the transition zone from fibrocartilage to ligamentous attachment using scanning electron microscopy, and 3) determine the mechanical properties of the transistion zones into the subchondral bone at the nanolevel and the concentration of chondroitin sulfate in these zones. The results will then be used to quantify a relationship between the structure and function of the native meniscal attachments and validate the current finite element model of the attachments. This data can then be used to develop, design and evaluate the meniscal replacements, including tissue engineered constructs. A successful meniscal replacement will work to prevent joint degeneration following meniscectomy.
Multiscale Modeling of the Effects of Physical, Chemical, and Hydrothermal Aging on Failure of Graphite/Epoxy Composites: Graphite fiber/epoxy composites are one of the primary structural materials used in modern civilian and military aircraft. Their excellent specific-stiffness and specific-strength properties are due to a sophisticated microstructure on constituent materials. However, the presence of the complex microstructure leads to several possible failure modes, including the formation of craze zones in the polymer matrix and the degradation of the polymer/fiber interface. Furthermore, the potential for mechanical failure of these materials increases significantly when they are exposed to elevated temperatures and possibly moisture for long periods of time (aging). An improved understanding of the failure modes of aged composites at the atomic level can lead to improvements in the development and durability of graphite/epoxy composite materials used in many aircraft structures. The development of a multiscale modeling approach that relates physical, chemical, and hydrothermal aging mechanisms on the molecular level with mechanical behavior of graphite/epoxy composites on the structural level. Specifically, the modeling approach will predict the onset of crazing in the crosslinked epoxy resin, the elastic properties of the epoxy resin, and the stiffness and strength properties of the fiber-matrix interface in graphite/epoxy composites as a function of aging level and type. The results of this research can be used directly in current NASA damage models to assist the agency in understanding and predicting the effects of aging on current and future civilian and military aircraft.
|
Features
Dr. Greg Odegard of the Multiscale Sensors and Systems research group. His research interests include multiscale computational and experimental mechanics, computational chemistry, materials science, and biomechanics.
See more in article "A Sense of Possibilities" PDF |
The Mechanics of Multiscale Materials (MMM) research group uncovers the relationships of structures across the full range of engineering scales, from the molecular to the macro.
Mechanics of Multiscale Materials PDF Article |
Graduate
Student Diego Villegas is looking at meniscal attachments
samples using the light microscope and a Canon camera attached.
See the article:"It's all in the knees" from the
College of Engineering newsletter 'Mechanics
of the Meniscus' PDF feature story
57 kb
|
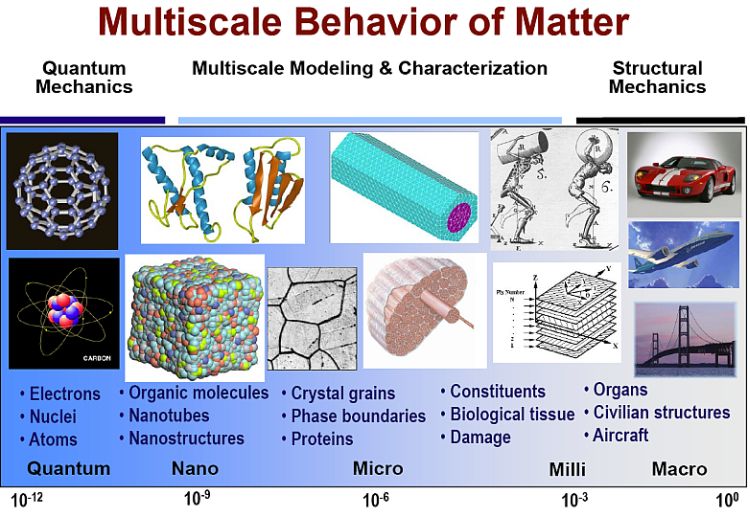 |
|
|